A guide for asset-heavy organizations seeking to invest in Asset Performance Management software, based on the findings of the Verdantix Green Quadrant: Asset Performance Management Solutions 2022 report. Get your copy of the report →
Asset Performance Management (APM) software is a critical component as industrial companies develop a safer, more efficient, more sustainable industrial future.
APM Software defined:
“Industrial software applications and associated asset content that monitor asset performance, predict failures and synchronize with IT and OT systems to generate insights that help optimize production, reliability, maintenance and environmental KPIs.”
Verdantix published a Green Quadrant report to provide decision-makers with a fact-based comparison of APM vendors on the market today. We’ll be highlighting some of the key takeaways from the report, and why asset-heavy companies must begin by solving the industrial data problem.
The evolution of APM software
Asset Performance Management is nothing new within the world of industry. For decades, firms have been investing in technology to help people optimize the way they execute reliability, maintenance, and operations. Based on studies about the adoption of APM software over the past 20 years, it’s clear that many of today's solutions are failing to meet the needs of industry:
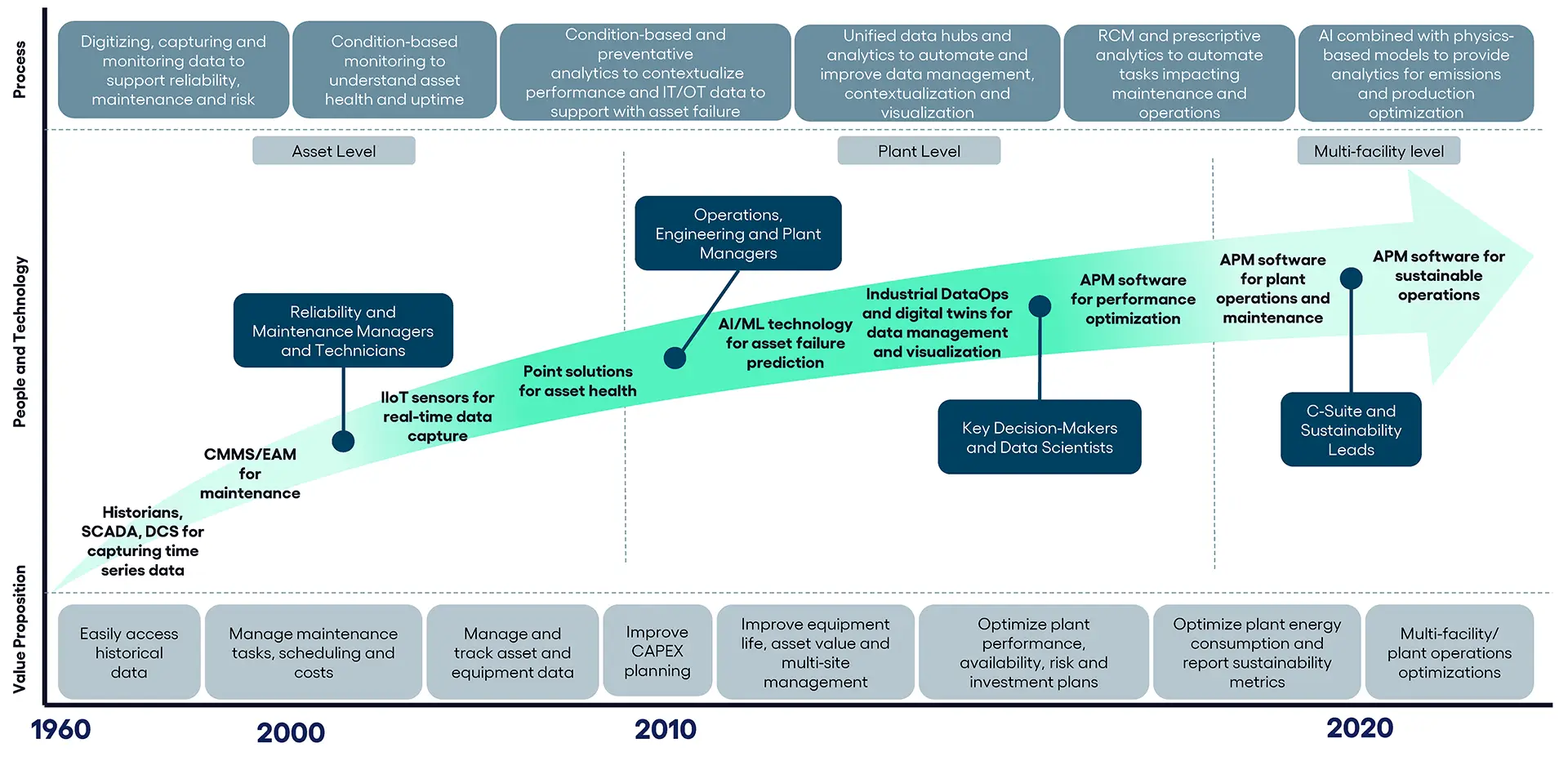
Evolution of Asset Performance Management
Verdantix findings
What it means for your organization
“Traditional solutions to support asset maintenance activities no longer meet business needs.”
Condition-based maintenance tools don’t provide enough insight; asset-heavy companies need APM solutions built on predictive and prescriptive models.
“APM solutions remain under-utilized across the process industries.”
Previous failures and implementation complexities, like the industrial data problem, limit APM software adoption both across operations and across sites.
“Software uptake is impeded by buyers not understanding the benefits.”
APM software encompasses much more than just predictive maintenance. APM solutions improve asset reliability and uptime, as well as performance efficiency, asset lifecycle management, sustainability, and more.
“Functionality has evolved to support maintenance, operations and sustainability.”
Pressures from cost-savings, sustainability requirements, and competition have forced APM software to evolve and become more robust by leveraging advanced data and analytics.
Asset performance management consists of a broad family of distinct, yet related, use cases, many of which are outlined below. These use cases may also have multiple digital components (dashboards, models, reports, etc) that must be developed, integrated, and maintained in order to solve the use case and close the loop. As a result, industrial companies can have 100's of individual data-driven components that they want to deploy, but don't yet have an efficient means to develop.
Use case family
Description
Maintenance optimization
(High priority)
- Maintenance planning optimization, analyze and predict maintainability, and forecast and optimize spare parts
- Support for industry standards and reliability-centered maintenance standards
Failure prediction
(High priority)
- Predictive analytics methods and tools to forecast asset failure and time-to-action for many asset types
- Prescriptive analytics are available to measure asset performance
- Trust in data to identify/avoid false positives
Reliability analysis
(High priority)
- Reliability life data analysis and associated industry standards
- Accelerated life testing (ALT) analysis
- Support visualizing and automating the building of failure models, asset criticality analysis, and FRACAS
Integrity management
(High priority)
- Improve the scheduling of operator rounds to streamline data collection, as well as to support shift handover
- Manage device calibration activities
- Improve the planning, efficiency, and effectiveness of inspections
- Support for integrity operating windows (IOW) programs
Performance optimization
(Medium priority)
- Optimization of performance based on: availability analysis and throughput calculation, production loss analysis, production optimization, and insights into operational performance
Asset health monitoring
(Medium priority)
- Build and maintain an asset health database with health overviews of equipment and functional locations
- Failure diagnostics based on thresholds/rules
Risk management
(Low priority)
- Quantitative assessment of the risks of asset failure in terms of fatalities, injuries, and environmental damage?
- Hazard analysis and asset-related incidents
Asset lifecycle management
(Low priority)
- Ability to perform life cycle cost analysis for both near and long-term asset purposes
Environmental performance
(Low priority)
- Carbon emissions monitoring/reduction, leaks, and seeps management, and improving energy efficiency
- Support environmental program goals and certifications
The industrial data problem
Historically, the solution for solving Asset Performance Management use cases has been to invest in siloed systems (e.g., ERP systems), niche solutions (e.g., IoT Applications), or run multi-year “lighthouse” projects with little-to-no ROI to show after months or years of data wrangling and deployment effort. If it takes two years to deploy an APM application at your lighthouse facility, do you really have 100 years to wait until the same solution is deployed across the remaining 50 sites?
Other firms simply remain cemented in traditional paper-based or Excel-reliant processes, with data remaining tucked away in filing cabinets or in their digital cousins — data warehouses. Across the enterprise, collaboration is hindered, value is left unrealized, and organizations are never truly data-driven.
“In the past, we struggled with cumbersome and disjointed systems which made it hard to access data. We needed something that would seamlessly connect with SAP, MES [manufacturing execution system] and data historians, so that all data could be accessed from one place. This will enable us to effectively monitor asset health and understand when it is time to replace or maintain our assets” - Operations Executive
At the core of these issues is the industrial data problem: cross-department data silos, lacking context from undocumented data, inconsistent workflows, and a lack of successful cross-site scalability. To put it simply, most APM strategies don’t scale because people lack simple access to complex industrial data.
When people are spending 90% of their time searching, preparing, and governing data, there’s little time left to invest in gaining better, data-driven insights. Without a coordinated and collaborative data management strategy, APM initiatives will continue to fall short of their ROI expectations.
Solving the problem
A strong data foundation is essential for the deployment of advanced analytical tools.
So, what can industrial organizations do to address this problem? At Cognite, we believe APM can only be solved once data is contextualized in an Open Industrial Digital Twin. The Open Industrial Digital Twin is a platform to build, deploy, and scale many data-driven solutions across operations, maintenance, and reliability required to improve asset performance.
This approach involves aggregating OT, IT, and engineering data types and data sets related to a given physical asset or set of assets in a single, unified location. By bringing all data into a single repository and contextualizing it, companies can rapidly build and deploy APM solutions to improve the performance of their assets and the people who operate them.
Data management platforms help firms streamline the data capture, handling and contextualization processes, while accelerating time to value, cloud deployment and scalability.
This digital twin provides a single, trusted data foundation for operations and analytics across assets and facilities. It ensures industry experts spend minutes, not hours, to find and understand the data they need. Digital twins provide a means to codify domain expertise, continuously enrich your industrial data foundation, and leverage new technologies for better data capture and safer operations. And an open, extensible digital twin allows your organization to work with preferred industry standard tooling and visualization software, along with trusted partners.
By investing in an Open Industrial Digital Twin, your organization will prove value from day one with out-of-out-of-the-box solutions and capabilities, connectors to your existing systems, and an ecosystem of partners. You will also have the means and the confidence to achieve the goal of an autonomous, self-improving industrial future.
Learn more about Asset Performance Management.
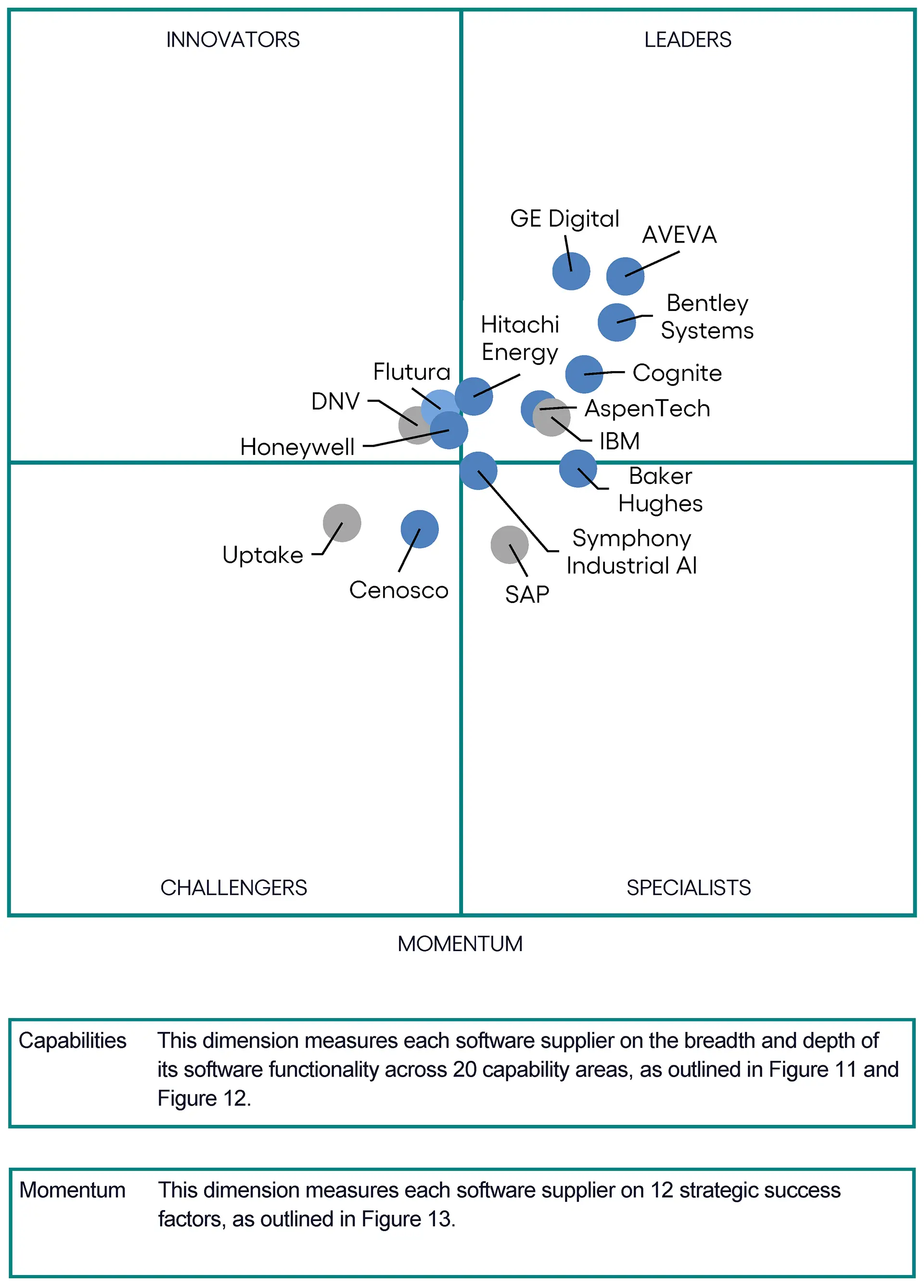
Green Quadrant: Asset Performance Management Solutions 2022