With the Metaverse estimated to be worth $2.5 trillion by 2030, according to Bloomberg Intelligence, are industrial companies ditching their Digital Twins and starting again, or is the Industrial Metaverse a modern-day Emperor’s new clothes?
Why is the metaverse relevant now?
Those of us who have been following Industry 4.0 technologies, trends, and hype, are all familiar with digital twins: virtual representations of physical equipment, assets, and processes that contextualize relevant industrial data in real-time to enable data-driven decision making, smart maintenance, and overall asset optimisation.
Learn more: Contextualized data and digital twins amplify digitization value
Much more of a newcomer — having blasted its way across the chasm from obscurity into mainstream business consciousness only last year in the tailwinds of social media platform Facebook’s rebranding to Meta, a metaverse company — is the industrial metaverse.
Is the industrial metaverse worthy of the hype, or is it just a glorified digital twin: the emperor’s new clothes?
Unpacking the industrial metaverse
The metaverse is an evolution of today’s internet, enhanced and upgraded to consistently deliver 3D content, contextually organized information and experiences, and real-time synchronous communication.
Figure 1: Industrial metaverse as a combinatorial innovation
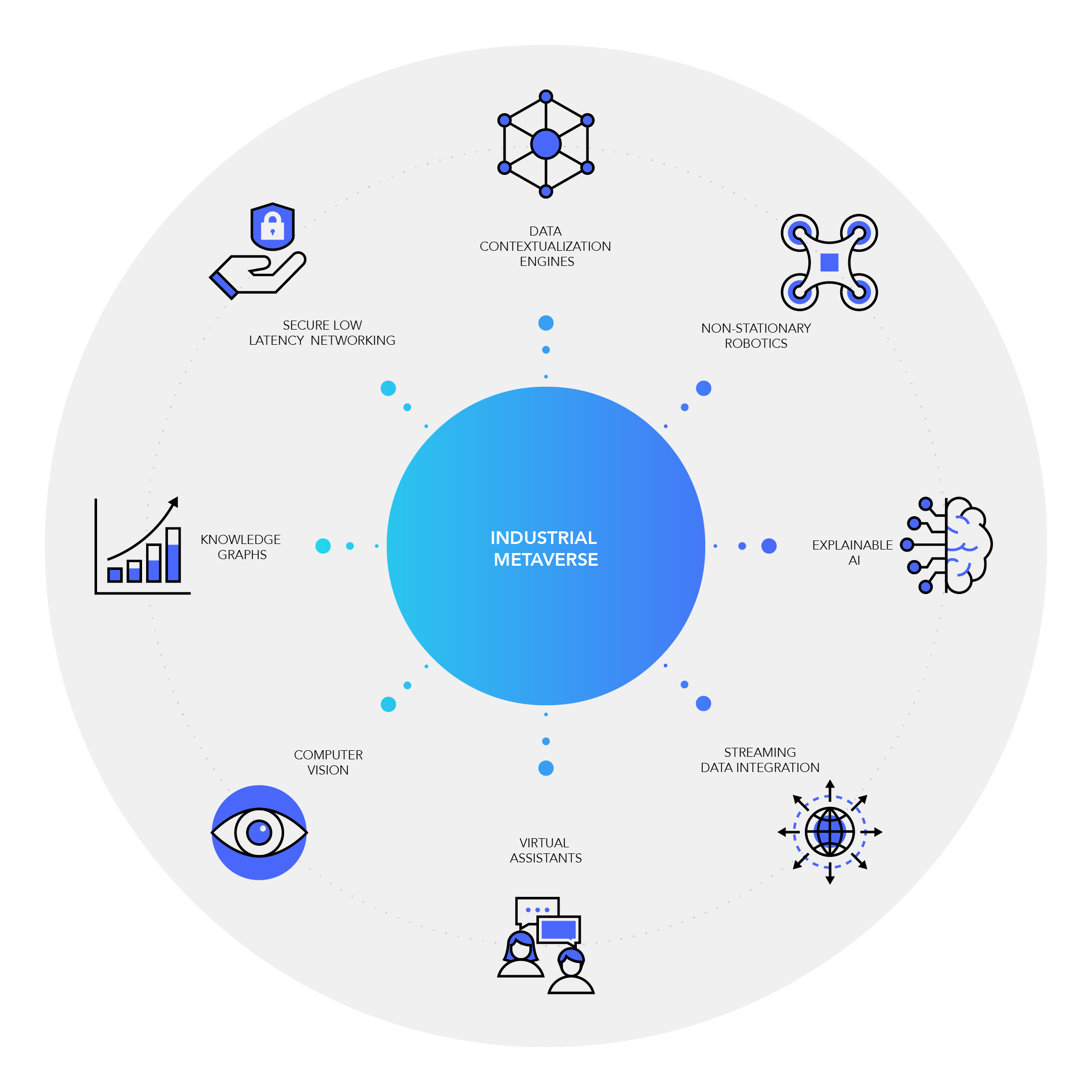
The metaverse will have both consumer and industrial orientations. In the consumer orientation, metaverse experiences are already playing out quite literally in the form of immersive online gaming universes, with retail and other entertainment experiences set to follow next. Conversely, the industrial orientation is set to impact how — and where — we work.
The industrial metaverse is a prime example of combinatorial innovation: the creation of new things through the mashup of different technologies with varying degrees of maturity. Whilst long-term implementations of industrial metaverse, and industrial metaverse ecosystems, are expected to fuse a dozen or more key digital technologies, the most important technological pillar are:
- Secure low latency edge and cloud hybrid networking, including public and private 5G networks
- Knowledge graphs to store entity relationships
- Data contextualization engines to automatically populate and refresh knowledge graphs (e.g. by recognizing things and events in the physical world, and linking them to contextually relevant data in the metaverse)
- Event streaming architectures for real-time notifications and ambient awareness based on relevance
- Computer vision (CV) and natural language processing (NLP)
- Explainable AI (whilst AI techniques will never be fully transparent, e.g. advances in physics-guided ML are greatly improving model accuracy as well as trust)
- Non-stationary robotics to automate data collection and routine inspections
- Blockchain and digital currencies for secure and frictionless transactions
- Virtual assistants to help navigate the information overload
But wait, isn’t above equally applicable to good old digital twins?
Google Maps remains the most impressive example of metaverse — and digital twin alike
Yes. Industrial metaverse is so close to its better known twin — the digital twin — that making a formal distinction between the two is splitting hairs.
Central to metaverse experiences is immersion in a virtual environment not only accurately mirroring the real world, but providing an analytically enhanced version of it. As such, Google Maps remains the most impressive example of metaverse.
Read also: The digital twin: the evolution of a key concept of industry 4.0
Industrial metaverse outlook based on a decade of digital twin experiences
As we await the singularity moment — the point in time when we spend more of work life within the virtual than the physical workplace — of the industrial metaverse to arrive, there are some learnings we can confidently extrapolate and layer onto the likely evolution of the industrial metaverse. The industrial metaverse will develop through a series of overlapping stages:
Figure 2: Industrial metaverse development outlook 2022-2030
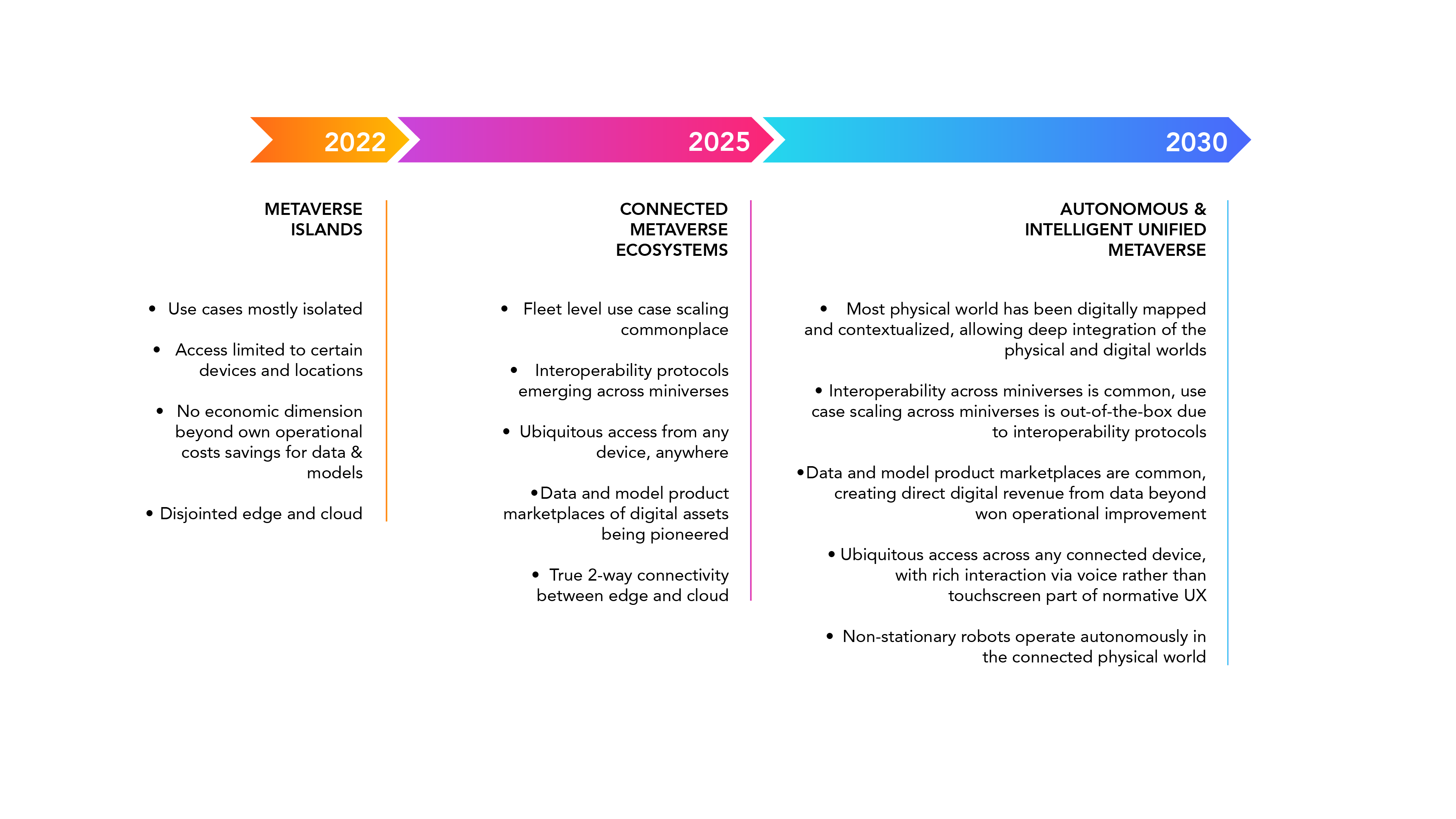
- Metaverse islands (now)- Productivity-enhancing use cases are isolated with little interoperability or transferability across assets, even within an enterprise’s own industrial metaverse (a miniverse). No active connectivity to others’ industrial metaverse islands- Access is limited to certain devices and locations, no real-time remote connection to physical assets beyond upstream sensor data flows- No economic dimension to industrial metaverse beyond own operational cost savings (no data product, or model, marketplaces)- Edge and cloud remain disjointed, with industrial metaverse experiences and use cases focused on cloud based executions
- Connected metaverse ecosystems (around 2025)- Use case scaling at the fleet level within miniverses is more and more commonplace- Protocols start to emerge to facilitate interoperability across miniverses- Access to industrial metaverses is ubiquitous from any device, anywhere- Data and model product marketplaces enable monetary assessment and trading/exchange of digital assets becoming common- Two-way connectivity between edge and cloud, creating a more dense intersection between the physical and digital worlds
- Autonomous & intelligent unified metaverse (late 2020s through early 2030s)- Most of the physical world has been digitally mapped and contextualized, allowing deep integration of the physical and digital worlds- Interoperability across miniverses is common, use case scaling across miniverses is commonplace- Data and model product marketplaces are common, creating direct digital revenue from data beyond own operational improvement- Access is ubiquitous across any connected device, with rich interaction via voice rather than touchscreen part of normative UX- Non-stationary robots operate autonomously in the connected physical world
Industrial metaverse in action - a scenario
Even with today’s digital twins, to perform maintenance or operations on critical assets engineers and SMEs typically have to travel to the site. This is time-consuming, expensive and often inefficient as without an accurate understanding of the issue before arrival, the correct tools and parts for repair may be unavailable.
Within the industrial metaverse, domain experts can be called onsite virtually from different locations to collaborate or solve an incident, using headsets to check the condition of assets, monitor machine and equipment data, and take corrective actions in real time, remotely.
Multi-functional teams, from operations, engineering and procurement for example, can discuss equipment or production problems, or review the energy consumption and water usage of a facility. The immersive environment of the Industrial Metaverse will enable visual investigation of an incident as it emerges, taking corrective action before costly downtime or substandard product is produced. Precise, virtual representations of the plant, asset, or machine can be simultaneously enriched with live feeds from cameras and robots. Access to this real-time data feed can guide the remote control of robots and drones that read both analog equipment (such as gauges) and digital instruments (stream videos or pictures), and perform maintenance operations as required.
The Metaverse will evolve into an autonomous and intelligent immersive environment, blending automation and human intuition to quickly solve problems. Industrial companies will gain visibility of, and control over operations that contribute significantly to the bottom line, and provide the transparency necessary to measure, monitor and control their carbon footprint.
Don’t repeat the pilot purgatory of digital twins. Design with scalability and money in mind from the start.
Whilst the industrial metaverse may not be so different from a digital twin, we should take caution to not repeat the pilot purgatory of digital twins. This means design with scalability and monetization in mind from the start. Most importantly, design for:
- Ubiquitous access from any connected device for all employees
- User experience over technical sophistication hardly anyone can use
- Substantially non-linear cost of use case scaling
- Data and model product marketplaces
Read also: Industrial DataOps: The data backbone of digital twins
Article originally published at: https://www.capgemini.com/insights/research-library/data-powered-innovation-review-wave-4/