The digital twin: one of the most useful, insightful tools to drive industrial innovation and value.
The term “digital twin” has been around for 20-30 years, depending on who you ask. Originally, the idea about digital twins came from the manufacturing world; more specifically, from a 2002 article in an academic journal that talked about “the idea that information about a physical object can be separated from the object itself and then mirror or twin that object.”
Today we know the digital twin as a combination of one or more data sets and a visual representation of the physical object it mirrors. But while the digital twin concept is no longer new, its meaning continues to expand based on technological advancement, particularly in the realm of the Industrial Internet of Things (IIoT).
Over time, digital twins have morphed to meet the practical needs of users. In oil and gas, for example, the possibilities of condition-based monitoring and predictive maintenance have amplified the need for a digital representation of both the past and present condition of an object or system.
Read more: The digital twin: The evolution of a key concept of Industry 4.0 →
Digital twin technology is changing: Introducing the Operational Digital Twin
It's possible for a company to enhance the overall understanding of its operations by putting all OT and IT data through a contextualization pipeline to create an operational digital twin. Here's our definition:
What is an operational digital twin?
An operational digital twin is the aggregation of all possible data types and data sets, both historical and real-time, directly or indirectly related to a given physical asset or set of assets in a single, unified location.
The collected data must be clean and contextualized, linked in a way that mirrors how things are or would be linked in the real world, and made consumable depending on the use case.
This next frontier in the digital twin space uses scalable cloud architecture to decouple individual models (e.g., applications, simulation models, and analytics) from separate source systems, reversing the unnecessary complexity established in point-to-point integrations.
The operational digital twin allows for data consumption based on the use case. Any model the user creates can live off the streaming live data that exists there, enriching the space by feeding its own insights or derived information (for example synthetic temperature or flow information created by a simulator for equipment where no real sensor exists) back into the twin. Combined with live and historical data, these insights on equipment behavior shore up the operational digital twin, making it even more complete and useful for the future.
Learn more about Open Industrial Digital Twins →
Digital twin examples
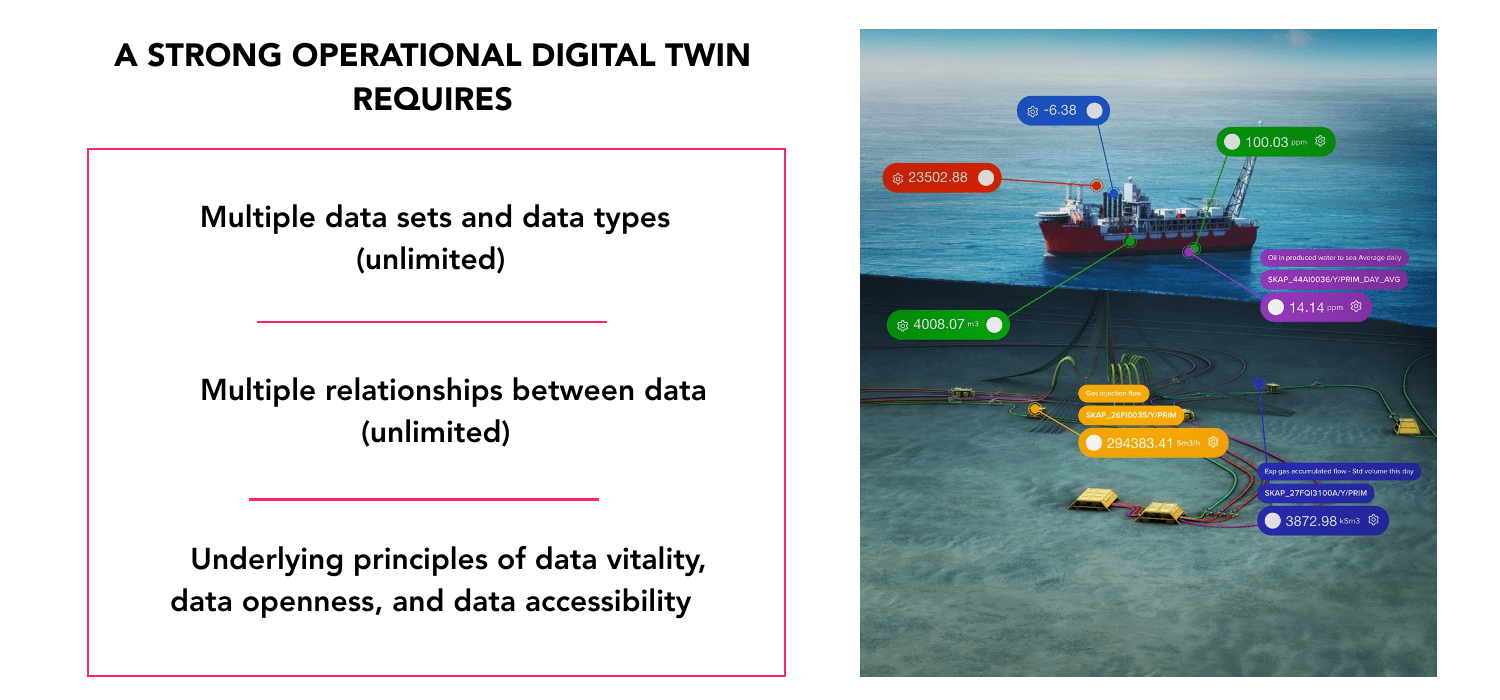
Cognite’s work with Aker BP, one of Europe’s largest independent oil and gas companies, showcases the potential of an operational digital twin. Since Cognite became Aker BP’s main technology partner in 2017, the two companies have worked together to decrease the cost needed to solve digitalization use cases and increase the scalability of solutions.
Aker BP’s tenant in Cognite Data Fusion® now contains more than 260,000 time series, 1.5 trillion data points, 700,000 documents, and 30 million events. The data used to be locked in disparate silos. Now it’s available whenever and wherever workers need it, powering solutions that are helping Aker BP cut costs, optimize production, revamp maintenance routines, reduce emissions, and increase worker safety.
Here are some of the use cases enabled by Aker BP’s operational digital twin:
- Combining physics and domain knowledge in a smart monitoring system that optimizes produced water disposal →
- Using data and applications to lay the analytical foundation for major emissions cuts →
- Calibrating multiphase flow meters (MPFMs) with an algorithm-driven method that dramatically decreases deferrals and losses →
Digital twins are here to stay
The research and advisory firm Gartner predicts that 'by 2023, 33% of owner-operators of homogeneous composite assets will create their own digital twins, up from less than 5% in 2018' while 'at least 50% OEMs´mass-produced industrial and commercial assets will directly integrate supplier product sensor data into their own composite digital twins, up from less than 10% today'.
In the same report, Gartner indicates that digitalization will motivate industrial companies to integrate and even embed their digital twins with one another to increase their own competitiveness. To do that, industrial companies need to make some sound strategic decisions now to lay a firm but flexible foundation for digital success.
Oil and gas companies that deploy an operational digital twin will finally have true control over their data—the ability to understand where it comes from, how reliable it is, and how to enrich it over time. They will also be the first ones to scale successful solutions on top of that data, which must be the priority of any digitalization initiative.