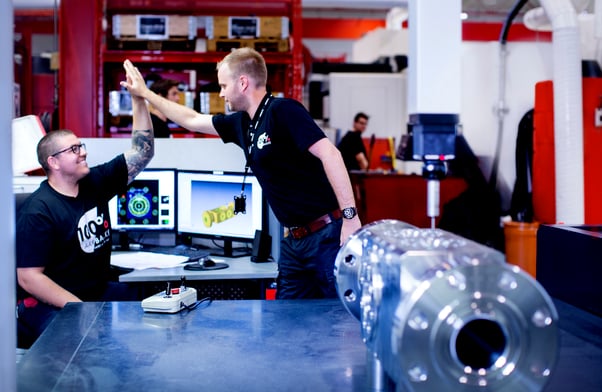
Outside of Stavanger, Norway, in a town called, Bryne, there’s a company that is making its factories not only smart. It’s making them learn. Listen to the full episode below or read on for the highlights.

With roots going back to 1918, Aarbakke manufactures parts and systems for Norway’s energy industry. Today, the company prides itself in having been built on Norway's rich industrial heritage, all the while having become a leader in manufacturing and digitalization.
Rolf Thu, Head of IT and Smart Factory manager for Aarbakke, spoke with us about how Aarbakke has taken its digitalization bull by the horns and what he sees coming next for the manufacturing industry. Our Q&A below:
Walk us through some of the innovations that Aarbakke is rolling out and what kind of impact you've made.
RT: We started adding digital tools to our operations back in 2003 - using tools that helped us monitor hydrolyzation in our machines. We’ve also gone into robotics, 3D printing, and 3D scanning for product quality verification. We’ve expanded to include digital documentation, and have connected our machines and systems in a new way - with Cognite - in order to see all of our data in context.
Data in context enables us to see our pain points. It tells us where we have the potential to improve how we use our machines, how efficiently we can operate them, and the flow of the products.
There’s so much data that is generated from our machines. We’ve got hundreds of tanks per machines and 40-50 connected machines. All that data was previously lost, but now we can see it in context with data from all of our systems, whether they’re monitoring, engineering, or maintenance systems.
This gives us almost unlimited possibilities to improve on our processes. To be able to see which tools have the best potential for optimization -- and which products we are wasting time on -- are some of the biggest upsides to this. We can think outside of the box in how we produce stuff. We can do more with our data.
So, you can also measure the impact of the innovations you’re making.
RT: Yes, this is key. We can measure the current state before making changes and to measure the act of the change. We can ensure that the use cases we employ add value, and we can see how things are working and make adjustments. We embed a kind of continuous learning into the mix. The common term these days is “Smart Factory,” but we like to think of what we’re doing as turning our “Smart Factory” into a “Learning Factory.” There is so much more value to realize from an asset that can learn too.
In your view, what are some of the biggest and best manufacturing industry innovations to date?
RT: The biggest changes are digitalization. Our partners and competitors are at varying stages of their programs. Some are slower, others are more on the leading edge. The leading edge is where Aarbakke needs to be and where I think we are. Looking at agriculture and farming, where we are now with digitalization is like when farmers began using tractors instead of horses.
In manufacturing specifically, we see a lot of interesting technologies that will challenge the old guard. We’ll continue to see a more complex, advanced way of manufacturing parts -- combining additive and metal removal manufacturing.
I suspect we’ll have smaller lot sizes as we become able to produce parts and equipment on demand. And then industry players will have to be competitive in producing very few parts at the same cost as they do in mass production. There will be less standardization and more parts made to order because we can be more flexible with new technology.
We’ll also see more machines automated, their programming done in the cloud, and a tight integration between customers and suppliers. The manufacturing world will see a more interwoven value chain and customer journey -- starting with where customers can upload 3D models for you, you then make the program, make the part and deliver it.
How are you keeping operations going under current circumstances?
RT: We actually saw more production value and throughput in the factory (in April) than we did before - forcing people to use IT systems and not take shortcuts or fixing an issue alongside the system. There have been learnings for us as well in management - to see the value in good data input and structured ways of using the systems.
When you’re forced to sit at a distance from colleagues, you are also forced to be more precise in inputting data, delivering messages and how you communicate. Nowadays, everyone has gone digital.
Note from the editor: Be sure to check out our full podcast channel with other episodes on Spotify and Apple.
All images courtesy of Aarbakke