日本触媒は2022年12月に、化学素材を製造する工場の生産性を高めるためにCogniteの製造業向けDataOpsプラットフォーム基盤「Cognite Data Fusion®︎」を導入した。まずはアクリル酸や高吸水性樹脂などを生産する姫路製造所に適用。その後、米国や欧州などの海外工場にも展開していく予定だ。現場作業員は、運転や保守などの作業を進める際、設備に関連するデータを検索することが欠かせない。これに費やす時間の大幅な削減と、さらに高度な分析の実施による予兆保全を含めた「生産性の向上」を狙う。
目指したこと:単なるデータレイクではなく
現在、DX(デジタル・トランスフォーメーション)の波が押し寄せている。具体的には、単なるデータのデジタル化だけでなく、デジタル化した様々なデータを有機的に結び付け、それを解析/分析して有効活用していこうという波だ。
DXの導入効果は極めて大きい。業務効率を改善できるだけでなく、より高度なビジネスモデルを遂行できるようになり、働き方の改革も期待できる。このため製造業の分野でも、すでに多くの企業がDXの導入に取り組んでいる。無論、紙おむつなどに使われる高吸水性樹脂の生産能力で世界トップシェアを誇る化学メーカーの日本触媒とて例外ではない。
同社は2021年に、2030年の目指す姿を描いた長期ビジョン「TechnoAmenity for the future」を発表し、「事業の変革」、「環境対応への変革」、そして「組織の変革」という3つの変革を目指すとした。また、2022年にはこれらの変革の実現を加速するため「DXビジョン」を掲げ、全社員がデジタル技術とデータを活用する環境の構築を急ぐ。
データ整理/加工に大きな手間
DXビジョンの実現。この役割を任されたのが中川博貴氏である。2022年4月1日付けでDX推進本部長に任命された。それまで同氏は、姫路製造所の生産管理センター長を務めており、製造所の活動の一環として生産現場の業務改革を推進していた。
ちょうどその頃の話だ。IT業界を中心に「ビッグデータ」というワードが注目を集めるようになった。そこで姫路製造所でも、同氏を中心に「ビッグデータ活用ワーキンググループ」が組織された。その中で「統合生産制御システム(DCS )が出力した運転データや、様々なイベントデータを解析/分析すれば、隠れているトラブルのタネをいち早く見つけ出し、『予兆保全』」が実現できるかもしれない」などの新しいアイデアが出てきた。
こうした新しいアイデアを実現したりできる最適なツールは存在しないのか。同氏はそれを探すために展示会に足を運んだり、インターネットで調査したりした。その結果、いくつかのツールに出会い、その中には導入を目的としたトライアルに進んだものもあった。
しかし残念ながら、いずれも導入には至らなかった。理由はすべて同じである。ツールに投入する前のデータ整理/加工に膨大な労力が必要で、生産現場の負担が重すぎたことだ。それと同時に、姫路製造所の生産現場では「データのサイロ化」という問題を抱えていた。DCSの運転データや保全履歴/故障情報データ、点検写真などはデジタル化されているが、そうしたデータはそれぞれに最適化したシステムに保存しているため1つの画面でシームレスに扱えない。配管計装図(P&ID)はPDF化にとどまっており、設備などの仕様書に至っては依然としてファイルに綴じて保管していた。
海外工場のトラブルも日本から対応可能に
その後、姫路製造所ではデータのサイロ化問題などを解決するために「情報統合基盤の構築」に取り掛かり始めたが、課題の整理はされたものの解決の糸口はなかなか見つからない状況だった。
就任にしてからわずか1カ月後のことだ。システムベンダーからメールで案内された 「予兆保全」や「データ活用」という言葉に興味を持ち、Cogniteが主催するウェビナーに参加した。お目当ての講演は、日本触媒と同様の事業も手掛ける総合化学メーカーの旭化成によるデジタルツインの構築事例に関するものだった。構築には、Cogniteが提供するDataOpsプラットフォーム基盤「Cognite Data Fusion®︎」を活用したという。興味深い講演だった。特に目を引いたのは、パソコン上のP&IDに書かれた装置/計装シンボルや配管をクリックすると、それに関連する様々なデータが次々と表示されるデモだった。まさに、これが欲しいものだった。
その後、Cognite Data Fusion®︎とライバル関係にあるツールのほか、コンサルティング企業から提案を受けたカスタムメイドによるツール構築なども一通り調査した。しかし同氏によると、「Cognite Data Fusion®︎は明らかに他を上回っていた。欲しい情報にたどりつくスピードが圧倒的に速かった」という。これで同氏の心は決まった。その後、姫路製造所と本社の担当役員を含む主要関係者の同意を取り付け、PoCを実施して機能や性能を検証した。そして最後に意思決定機関の了承を得て、2022年12月に正式な導入が決まった。
主要な結果
初期導入の作業は、Cogniteから派遣されたエンジニアの支援を受けて3カ月間で実施した。具体的には、姫路製造所にある約70カ所ある生産プラントの中から12カ所を選び、運営に関わる主要データ群(設備データや運転データ、図面データ、保全データなど)をCognite Data Fusion®︎に取り込み、関連付け作業を実施した。その後、各プラントを担当する現場作業員(プラントオペレーターなど)が実際に運用を開始した。「現場の評判は非常に高く、主要データ以外の取り込みや、全プラントへの展開を求める声が数多く届いた」(同氏)。
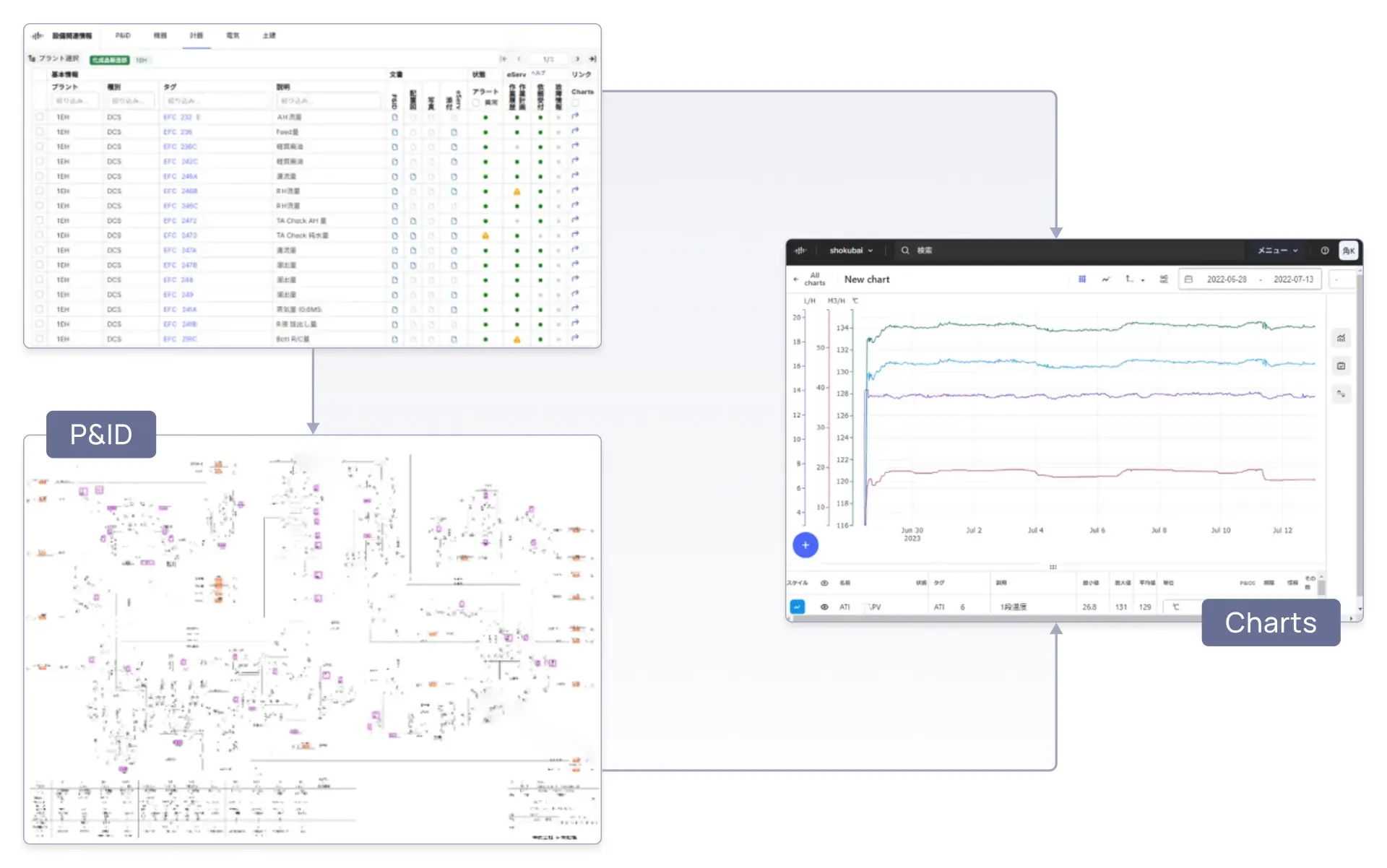
配管計装図(P&ID)上で複数の計器を選択すると、それらの計器で測定した結果をまとめてチャート化できる。Cognite Data Fusion®︎への登録作業が済んだプラントでは、すでにこうした機能が利用できる。なおこの機能は、Cogniteによって作成された日本触媒向けカスタムアプリである。
こうした声に応えるように現在、姫路製造所ではCognite Data Fusion®︎導入の担当者を任命し、Cogniteのエンジニアの支援を受けることなく、姫路製造所にある全104カ所の設備(プラントと用役設備の合計)に展開する作業を進めているところだ。同氏によると「2024年2月時点での進捗状況は約85%。2024年3月にはすべて完了する予定」という。
現在実施している主な作業は、Cognite Data Fusion®︎に取り込んだ情報の関連付けだが、その8割程度は、Cognite Data Fusion®︎に実装されたCognitive AI機能の支援を受けられる。もちろん残りの作業はある程度の労力と時間が必要だが、ほかのツールに比べれば大幅に少なくて済む。「産みの苦しみとして許容できる範囲だ」(同氏)
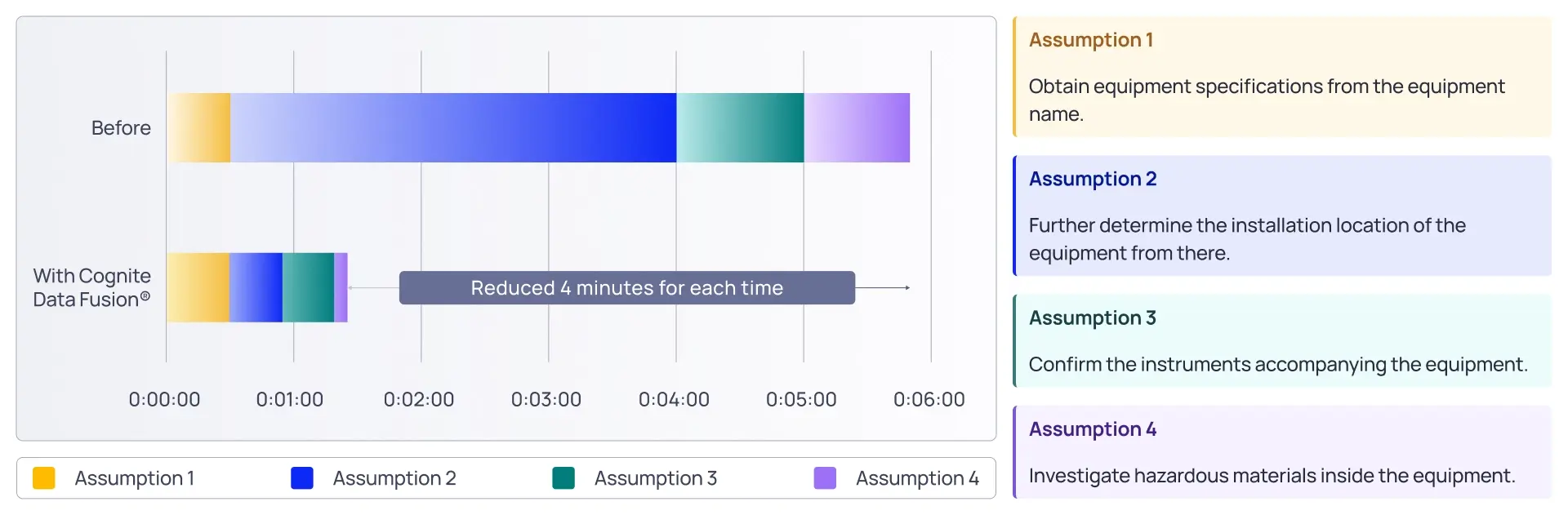
データ検索に費やす時間を大幅に削減できる、例えば、「想定1) 機器名から機器の使用情報を取得」「想定2)更にそこから機器の設置場所を知る」「想定3)更にその機器に付属している計器類を確認する」「想定4)更に機器内の危険物について調査」というデータ検索の場合は、「Cognite Data Fusion®︎」を使うことで従来に比べて4分強の時間短縮が可能になる。こうした時間短縮を積み上げると1年間に約9000時間になる。
同社は、Cognite Data Fusion®︎の導入効果として生産現場におけるプラント関連のデータ検索に要する時間を1年間に約9000時間減らせると試算する(図2)。その結果、生産現場の省力化が可能になるわけだ。「今後日本は労働生産人口が減少していく。それに対応する体制づくりが必要という背景もある」(同氏)。
今後同社はCogniteとの関係をより強化し、Cognite Data Fusion®︎の利用範囲を広げていく考えだ。方向性は3つある。
- 点群データやパノラマ写真を撮影してCognite Data Fusion®︎に取り込んで、Googleが提供する「ストリートビュー」の工場版のようなデジタルツインを実現することだ。現時点ではP&IDを出発点として、そこから様々なデータを引き出している。これをデジタルツインの中の画像を出発点として、同じように使えるようにする。
- ロボットの活用だ。例えば、ロボットが計器の設置されている場所まで移動し、表示部をカメラで撮影して数値を認識してデジタル化する。こうすれば、現場エンジニアの負荷を減らせるようになる。
- 海外展開である。海外工場にもCognite Data Fusion®︎を導入すれば、日本から海外工場の設備データや運転データ、図面データ、保全データなどを確認できるようになる。その結果、トラブルへの素早い対応などが可能になる。